Introduction
As global demand for sustainable manufacturing rises, understanding the materials that are at our disposal becomes essential. There are a number of materials in the plastics industry, however, one of the most fundamental distinctions is the difference between thermoplastic and thermosetting plastic. These two types of plastic products will determine the behavior, recyclable nature, usage, and life cycle of plastic products across most industries.
The difference between thermoplastics and thermosetting plastic is in their chemical characteristics and how each is affected by heat (or the process of heating). In short, can be reheated, remolded or molded repeatedly with no change to the molecular structure of the material while thermosetting plastics cannot be or remold again at any temperature once it is set. This difference between thermoplastics and thermosetting plastic drives decisions from packaging all the way through automotive applications.
This blog will cover the basic properties and difference between thermoplastics and thermosetting plastic, provide key examples, and list comparative benefits and detriments, and will then recommend which material is best for which applications.
What are Thermoplastics?
Thermoplastics are a type of polymer that become pliable when heated and harden when cooled. This is reversible for the same material without changing the inherent properties of the material itself. This characteristic is the main distinguishing factor between thermoplastic and thermoset.
Important aspects include:
• Reusability
Melted and remolded into different forms without deterioration.
• Chemical Structure
Linear and branched polymers with weak intermolecular forces.
• Environmental Benefit
Easier to recycle than thermosets.
Among thermoplastic and thermoset, thermoplastics are commonly used in packaging, bottles, automotive parts and medical devices etc. because of their flexibility and pliability. When choosing between thermoplastic and thermoset, industries factor in reprocessability.
What are Thermoset Plastics?
Thermoset plastics are plastics that permanently harden when molded and melted. Once set, they are not reformable. Among thermoplastic and thermoset plastic, thermoset plastic is more stable yet less flexible.
Important aspects include:
• Reusability
High resistance to heat exposure, wear, or chemical attack
• Structure
Cross-links between polymer chains are created through the curing process. Hence the thermoset plastic’s structure is irreversible once it’s molded.
• Recyclability
Unlike thermoplastics which can be re-melted and restructured, thermosets cannot be recycled by melting.
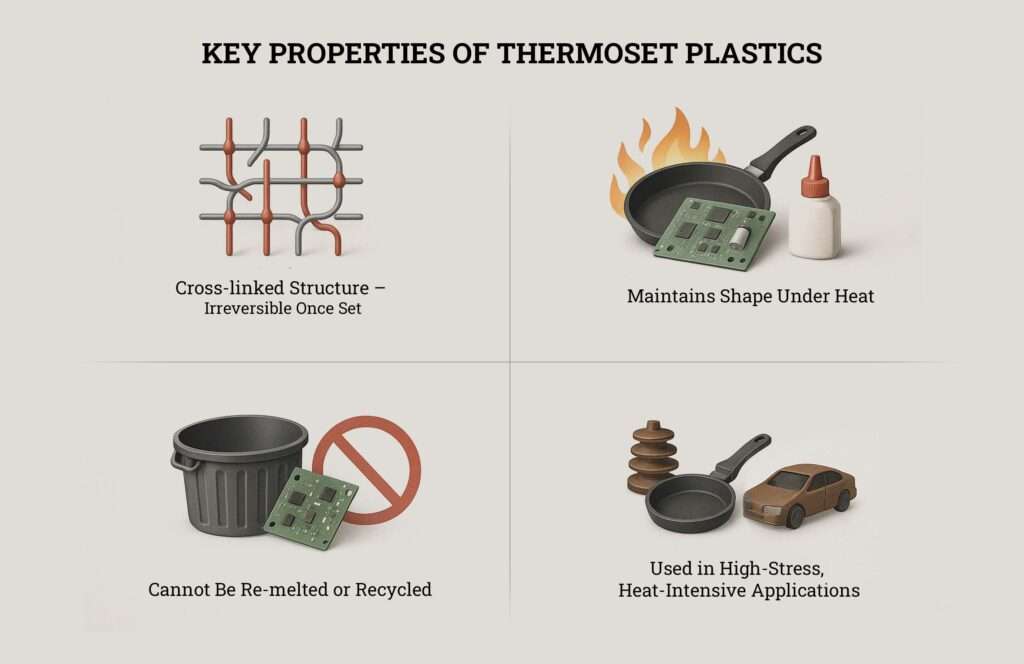
Between the two; thermoplastic and thermoset plastic , thermoset plastics are commonly used for electrical insulation, make household cookware, adhere, and also form components for motor vehicles where structural integrity and heat resistance are important.
Examples of Thermoplastic and Thermosetting Plastics
Understanding thermoplastics and thermosetting plastics examples aids material selection across industries. Flexibility, durability, as well as recyclability are determining factors for thermoplastics and thermosetting plastics examples.
Thermoplastics
• Polyethylene (PE)
Plastic bags use polyethylene (PE) as do milk bottles and packaging films. They are highly recyclable.
• Polypropylene inside (PP)
Food containers, automotive parts, and textiles have polypropylene inside. It has resistance to wear and chemicals.
• Polyvinyl Chloride (PVC)
Cable insulation and plumbing pipes are common use cases as it is tough and flame-resistant.
• Acrylonitrile Butadiene Styrene (ABS)
Helmets as well as appliances including LEGO toys utilize Acrylonitrile Butadiene Styrene and is known for impact resistance.
• Polystyrene (PS)
Lightweight and low-cost Polystyrene includes labware, disposable cutlery and packaging foam..
Thermoset Plastics
• Epoxy Resin
It’s used within electronics, adhesives, and protective coatings. Superb bonding properties.
• Melamine Formaldehyde
Scratch resistance coupled with high heat resistance, it is used for tableware, kitchen laminates, and furniture surfacing.
• Phenolic Resin
Known for electrical insulation Phenolic Resinis used in switches and circuit boards and handles can also use it.
• Polyurethane (PU)
Versatile and durable, it is used for mattresses, footwear and insulation foams.
• Unsaturated Polyester Resin (UPR)
It is tough and water-resistant and used for boat hulls, bathware, and automotive parts.
Thermoplastics and thermosetting plastics examples reflect their respective properties. Thermoplastics offer both reusability and flexibility while thermosetting plastic provides structural strength with thermal resistance.
Difference between Thermoplastic and Thermosetting Plastic
Property | Thermoplastics | Thermoset Plastics |
Heat Reversibility | Can be remelted | Cannot be remelted |
Bonding | Physical bonds | Chemical cross-linking |
Recyclability | High | Low |
Flexibility | Flexible | Rigid |
Cost | Often lower | Generally higher |
Applications | Packaging, consumer goods | Electrical, structural parts |
The difference between thermoplastic and thermosetting plastic is rooted in their structure and recyclability, which informs their functionality and disposal.
Advantages & Disadvantages of Thermoplastics
Advantages:
- Easy to mold and shape
- Recyclable
- Economical for large-scale production
- Lower processing temperature
Disadvantages:
- Lower thermal stability
- Can deform under prolonged heat
- Not ideal for high-load structural components
Advantages & Disadvantages of Thermoset Plastics
Advantages:
- High structural integrity
- Excellent thermal and chemical resistance
- Maintains form under stress and heat
Disadvantages:
- Cannot be reshaped after setting
- Recycling is limited and complex
- Higher energy and cost in production
Which Plastic is Best for Your Needs - Thermoset or Thermoplastic?
The choice between thermoset and thermoplastic depends on application needs:
Choose thermoplastics for consumer goods and packaging if cost-efficiency, recyclability, or flexibility is a requirement.
Choose thermoset plastic in the case of electrical parts or automotive parts when the requirement of the product is to endure high stress, high heat exposure or chemical exposure.
It is critical to select materials upon the requirement, use case and properties. When selecting between thermoplastic and thermoset, one must evaluate lifecycle, end-of-life management, and sustainability goals.
Conclusion
Engineers, product designers and professionals of sustainability can make more informed decisions if they learn the difference between thermoplastic and thermosetting plastics. With regard to material selection, this becomes particularly relevant as our industries evolve towards a circular economy and consumers begin to care more about sustainable products. An example would be thermoplastics due to their recyclability and cost, while thermosets have unmatched extreme durability and resistance.
To practice responsible processing of plastics, one must know how to retrieve their value and processes, sorting, and reintegration. When designing a product or even designing a recycling system bio mechanically, knowing your polymers is your first step to a cleaner and sustainable world.
Read more about types-of-plastics and know which are recyclable and which are not.
FAQ's
Why are thermoplastics better for the environment than thermosetting plastics?
Thermoplastics can be re-melted and reused, making them easier to recycle. Thermosets, on the other hand, require more energy and cannot be reshaped after setting.
Which type of plastic is better for high-temperature applications?
Thermoset plastics are more suitable due to their ability to withstand heat without losing form.
Which plastic type is more cost-effective for manufacturing?
Thermoplastics are generally more cost-effective for high-volume, low-cost applications.
Which type of plastic is more suitable for outdoor applications?
Thermoset plastics, thanks to their resistance to UV, heat, and chemicals, are typically better for outdoor applications.